Forensic Engineering
We do all we can to make sure the things we design are as unlikely to fail as possible by considering all the possible failure modes that may exist. We try to manage the risk but despite this, sometimes, unforeseen things happen with potentially dire consequences for our system or worse. Working back to reconstruct the chain of events may be required particularly if liability is a concern, but in all cases the knowledge gained in the process is invaluable because it teaches us how to improve the way we consider and manage the risks inherent in every system, product or component we design.
Engenya has worked on or conducted numerous failure investigations, both in commercial and legal contexts. Our work has been valued by our clients because of the solid scientific approach we take to proving our hypotheses for the root cause of any failure. We have helped clients overcome costly technical difficulties encountered in the normal course of operations by uncovering the underlying issues associated with system design and context, and we have provided unassailable arguments in situations where our clients have needed to defend their rights.
Methodology
Every failure reconstruction analysis is a systems problem. This is because context is an inextricable element in the failure event. For this purpose, we have adapted the engineering V-model for development to the investigation of the root causes of failures. This process is, naturally, adaptable to determining failure in order to rectify an engineering problem as well as for the purposes of assigning responsibility. Within this process, we apply any tools we require for the development of a hypothesis and its validation. Such tools may include various systems analysis methodologies, numerical simulation tools or testing. The diagram below represents our generic process for the determination of the technical causes of failure and their solution.

System Analysis
The systems engineering process, on which our forensic process is based, is described on our Systems Engineering page. Out of that process, some tools and methods are of particular relevance to the reconstruction of failure events. One such tool is context analysis. In the example, an oil field installation failure was analysed in its context to identify and prioritse potential failure modes. This resulted in the list of candidate failures being reduced to render the investigation process more efficient. If you are interested, more detail on this specific case can be found on our ESP Insertion Failure page.
Understanding the system’s context at the time of the failure event is crucial because many times the failure happens because of unforeseen events. Ultimately, the probability of successfully identifying the root cause is highly dependent on full disclosure of information and a thorough understanding of conditions. To extract this information, you have to ask the right questions. We know how to do that.
Detailed Analysis
Very often, it is impossible to reproduce the actual event or failure in the laboratory, and so we resort to engineering analysis, modelling and simulation. Engineering analysis and simulation allows us to reproduce events in a virtual sense, accounting for the full context and physical phenomena involved. In the simulation realm we are not constrained by safety concerns, reproducibility of extreme conditions or limits in resources. Additionally, if the point of investigation is the rectification of a technical problem, we can even validate the solution virtually to reduce the risk once it is deployed in the field.
Our strength in engineering analysis and simulation has made the difference for our clients on multiple occasions. Since we approach this with the utmost rigour, always advising our clients objectively, we have been able to provide winning arguments against opportunistic claims, to help our clients reach fair settlements and to solve purely technical issues in the most effective way possible. We have even had clients that after experiencing some tough lessons and subsequently learning what we could do for them, introduced our capabilities into their technical process as a risk management activity.
If you have not seen it yet, and are interested to find out more about this capability, please visit our Modelling & Simulation page. Incidentally, the accompanying graphic depicts the crushing of a charge carrier tube as a result of shock travelling through the system. Such an event would jeopardise the successful completion of an oil well.

Testing

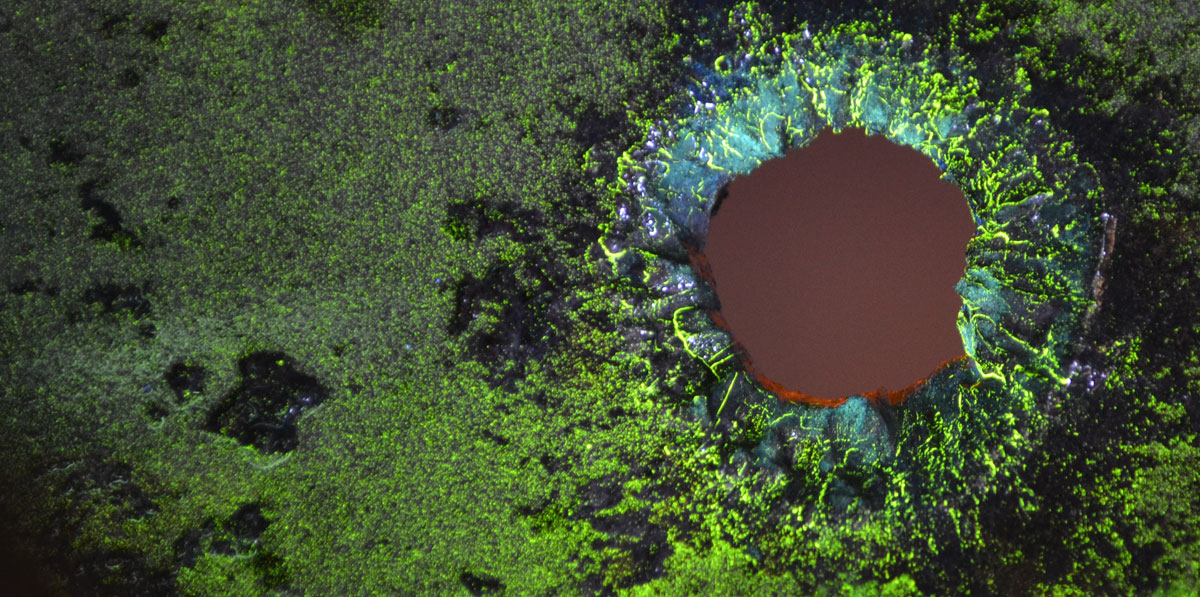
Demonstrating a failure hypothesis through testing is the ideal way to remove doubt about the root cause. While this is not always possible to do on a full scale, testing can always be employed to verify and validate parts of the hypothesis and to increase confidence in the conclusions.
We leverage our partner network as well as commercial laboratories to conduct testing when it is required. Engenya will design, plan, witness and document the tests required to verify modelling and to support the overall hypothesis. Testing may include metallurgical analysis, strength testing, fatigue testing, drop testing, functional testing, fatigue testing, vibration testing, field trials, etc.
Successful test campaigns are based on thorough preparation and are focused on reduction of uncertainty in key aspects of the investigation or design process. Determining what to measure and where, is usually done in coordination with simulations to ensure the highest fidelity and efficacy.
Reporting
The value of testing is captured in the test report. It is through this medium that the meaning of the test result is conveyed. Engenya focuses on presenting results in a way that is clear and easily understood both by experts and non-experts using a combination of clear text, custom graphics and supporting animations. Our reports have been praised by our clients for being clear and concise, whether delivered to a technical person or to a court.
