Gun Parting Failure

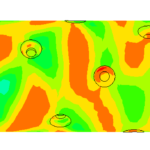


The perforation of an oil well is a highly energetic event. Think of thousands of small explosive charges releasing their energy in the space of tens of milliseconds, within the confines of a steel tube that in turn lies within a fluid-filled oil well not much bigger than the tube. The purpose is to “drill” holes into the oil bearing formation to enable its extraction. You can probably imagine that things can, and sometimes do, go wrong.
In the case described here, a medium length string experienced what is known as a gun parting failure. During completion, one of the explosive laden tubes fractured and parted, dropping the lower part of the work string into the well. This is a costly event if the loose portion of the string has to be fished out of the hole because it requires additional time to accomplish – and time is money. This is even worse if it happens on an offshore installation as rig and operations costs can easily soar into the millions. It is understandable, therefore, that there is a desire to determine the root cause of the event and whether it is an isolated occurrence due to prevailing conditions at the time, or whether it requires a design change on the next job.
After the separated part of the string was fished out of the well, the usual metallurgy investigations were conducted to conclude that a high speed fracture propagation had been responsible for the failure. The failed component is shown in the top picture. This conclusion enabled the formulation of a failure hypothesis and the consequent development of a finite element model of the perforation event. A simulation approach was selected to investigate the validity of the hypothesis because downhole conditions at the true scale of the problem are practically impossible to reproduce in surface testing.
Simulation consisted of the generation and solution of a fluid dynamics model of the gun interior during charge detonation (centre picture). The purpose was the generation of a dynamic pressure distribution on the gun’s interior and exterior surfaces at downhole conditions. This dynamic pressure distribution was then mapped onto a structural model of the failed gun and the stress dynamics calculated. An example of a resulting stress pattern is shown in the last picture (deformation magnified). The shape of the calculated stress concentration was shown to be remarkably similar to the shape of the failure surface. Interestingly, this shape was repeated at each charge location, with the difference in intensity being made by the constructive and destructive interference of the stress waves moving up and down the structure.